Ten10 Video FAQs
Helpful and instructional videos from Ten10.
Helpful Ten10 Videos
Ten10 Video Playlist
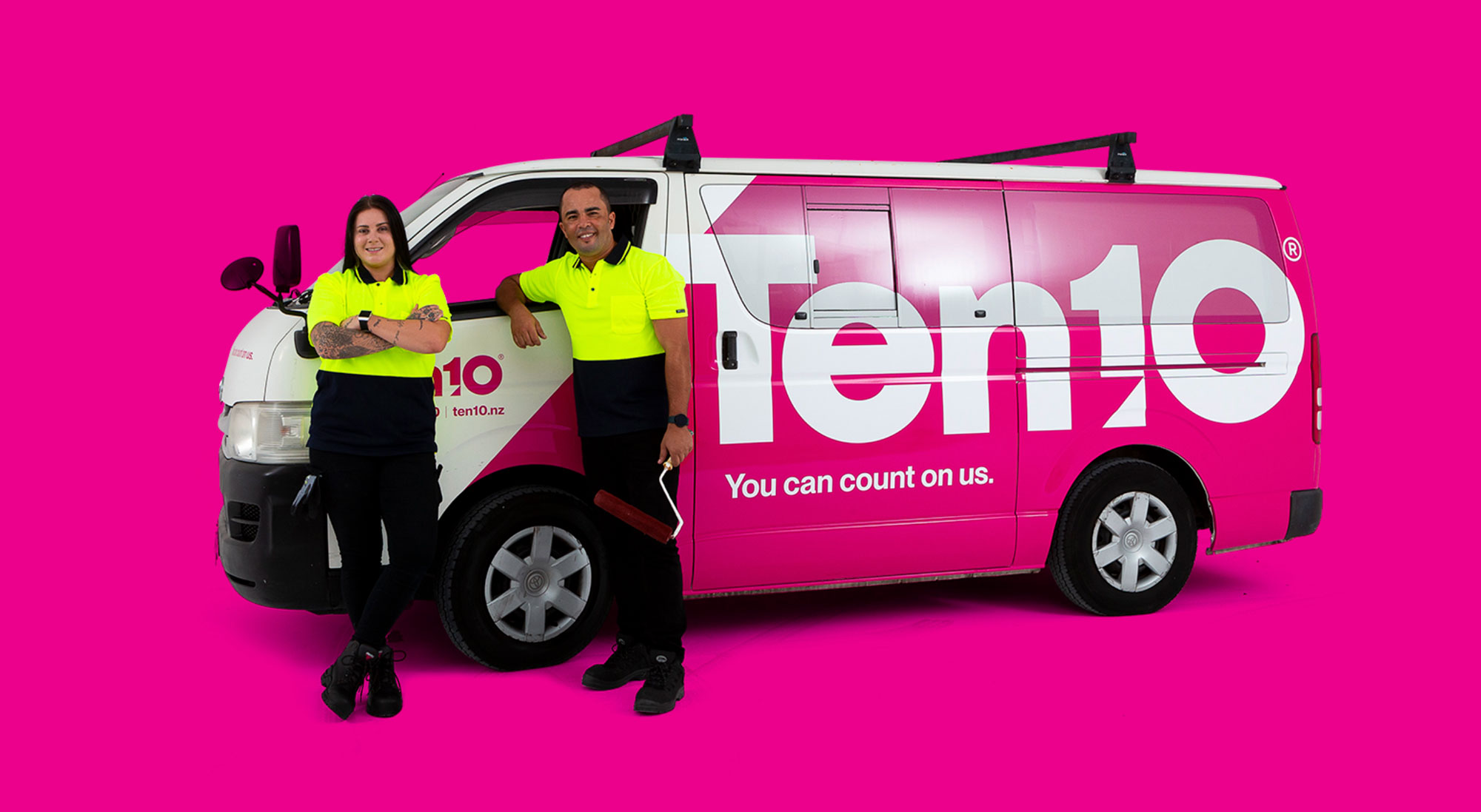
0:46
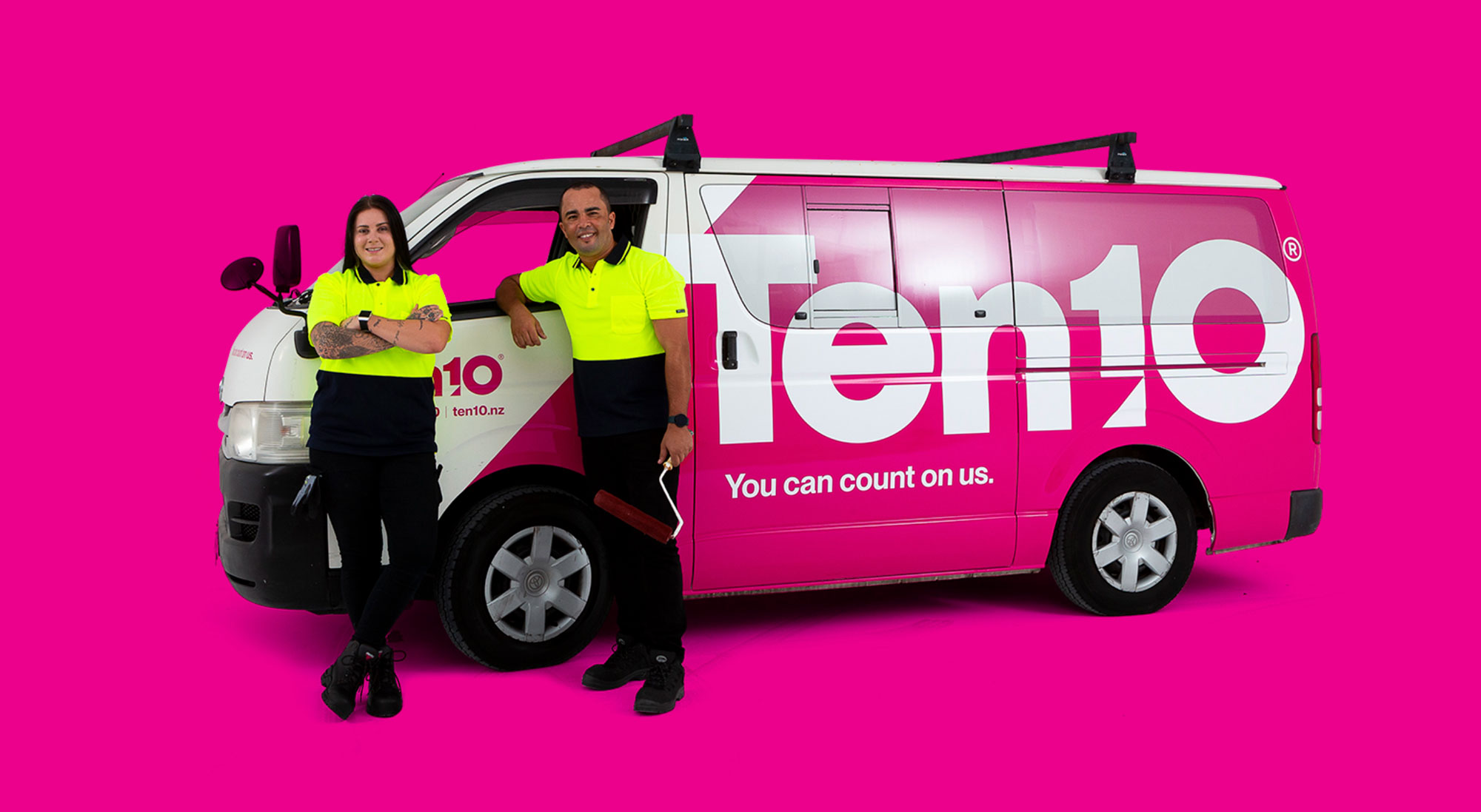
0:47
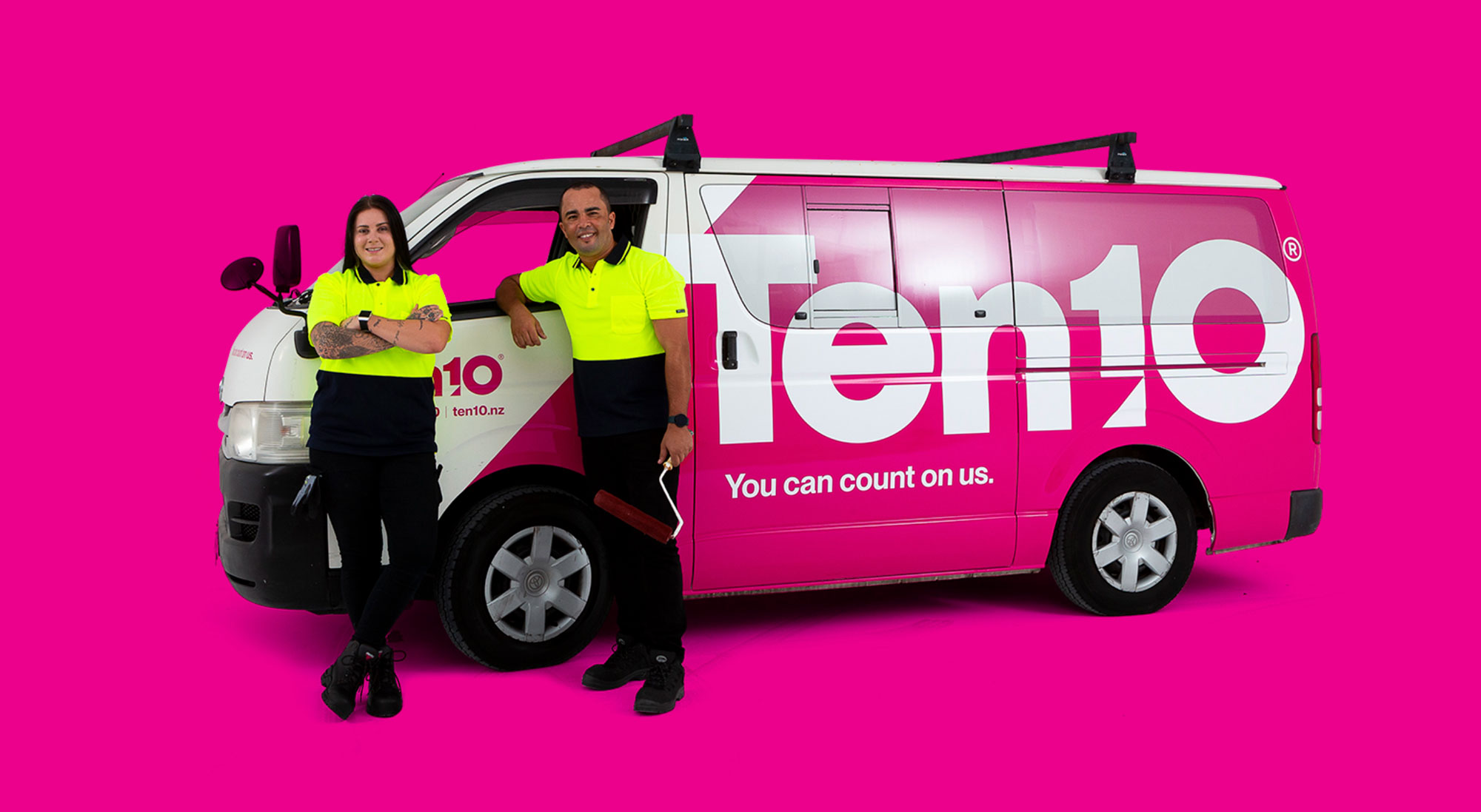
0:56
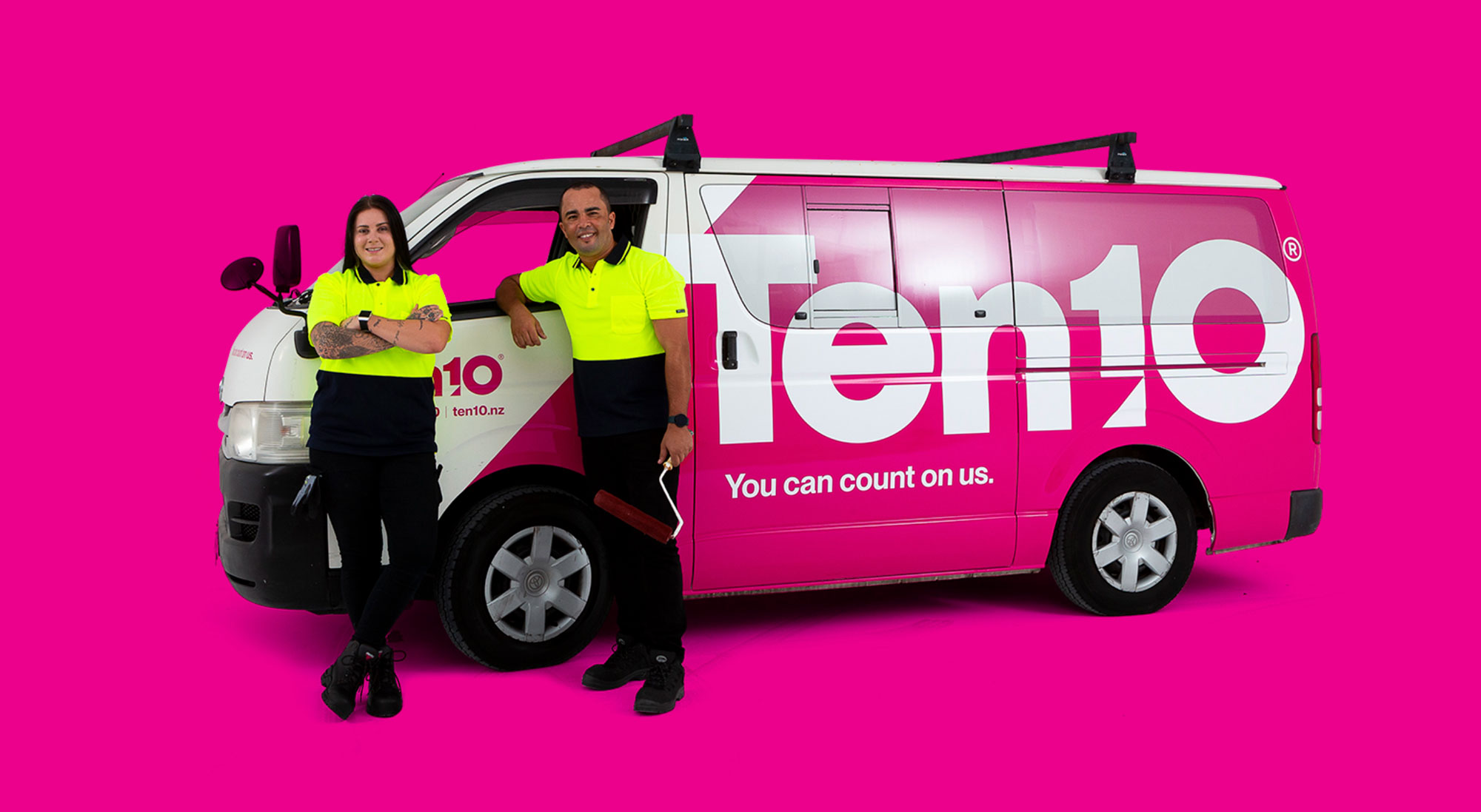
0:52
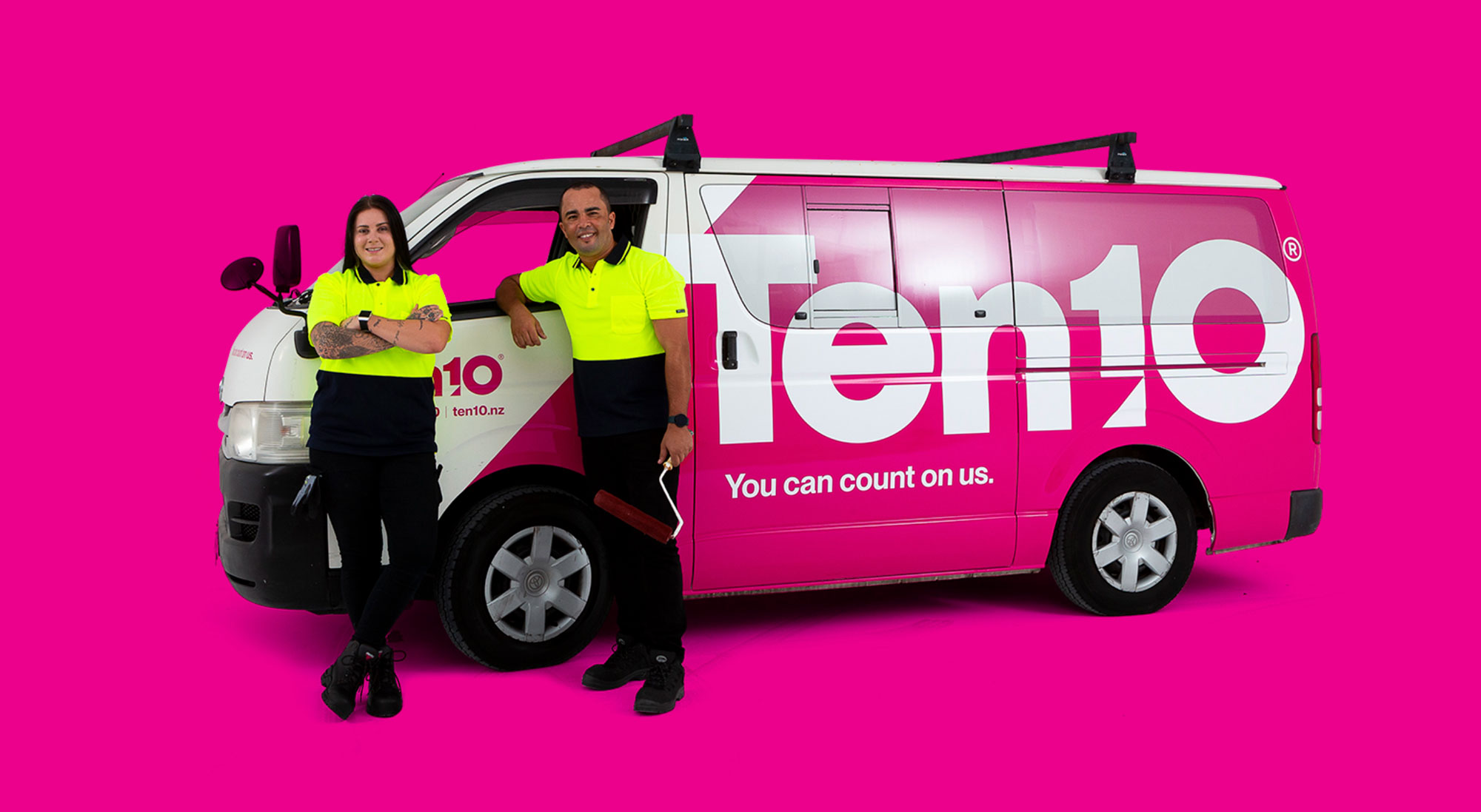
1:55
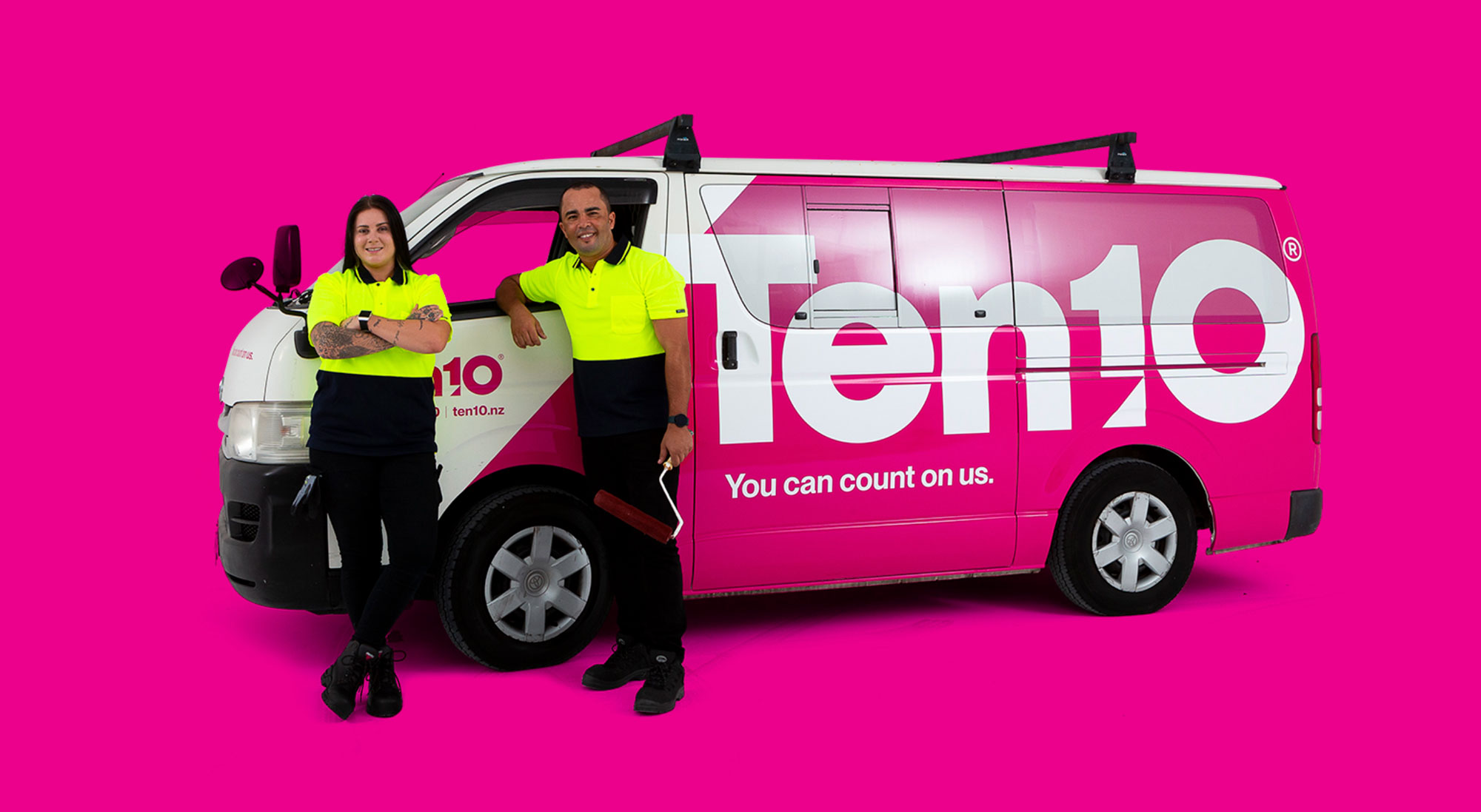
1:31
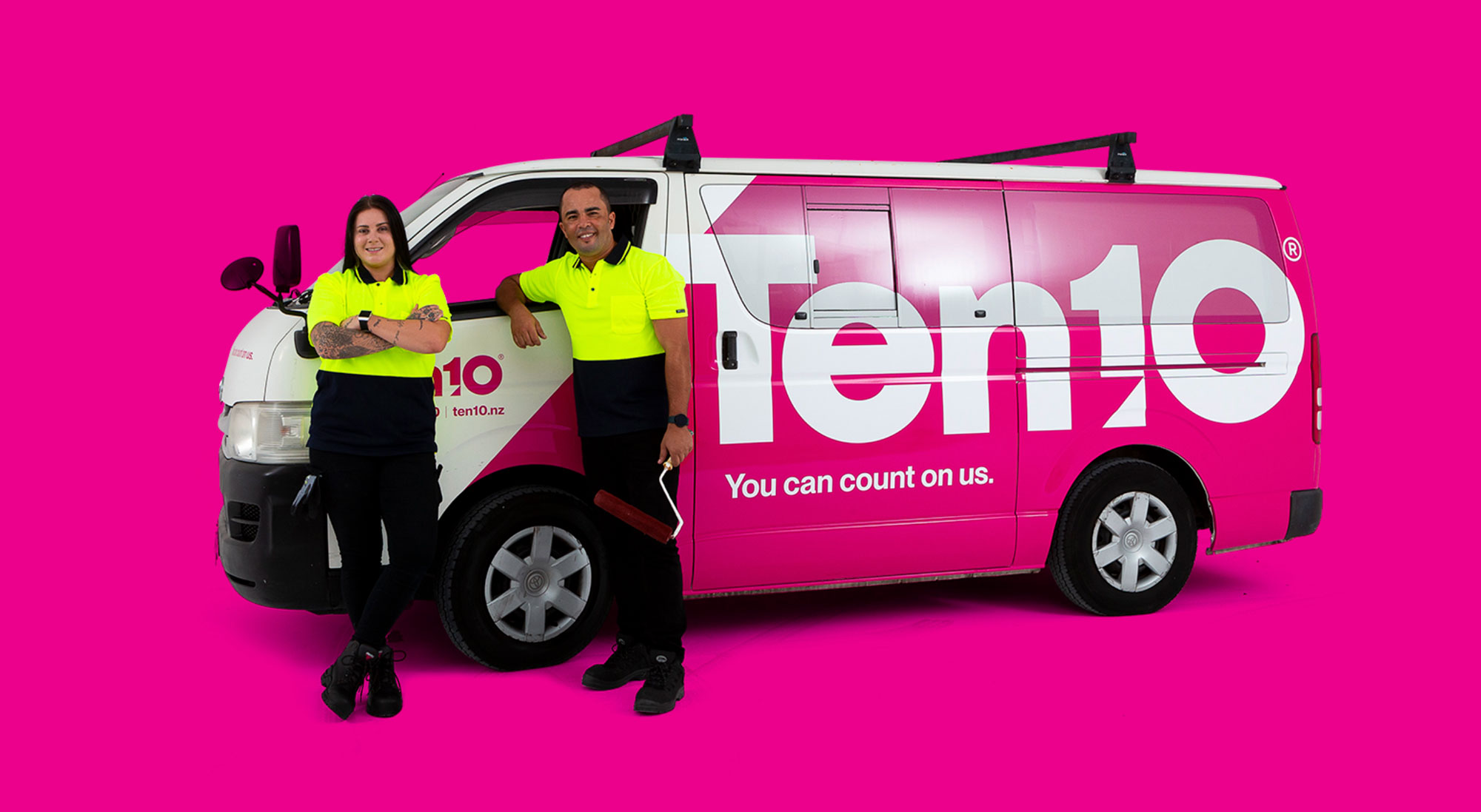
1:10
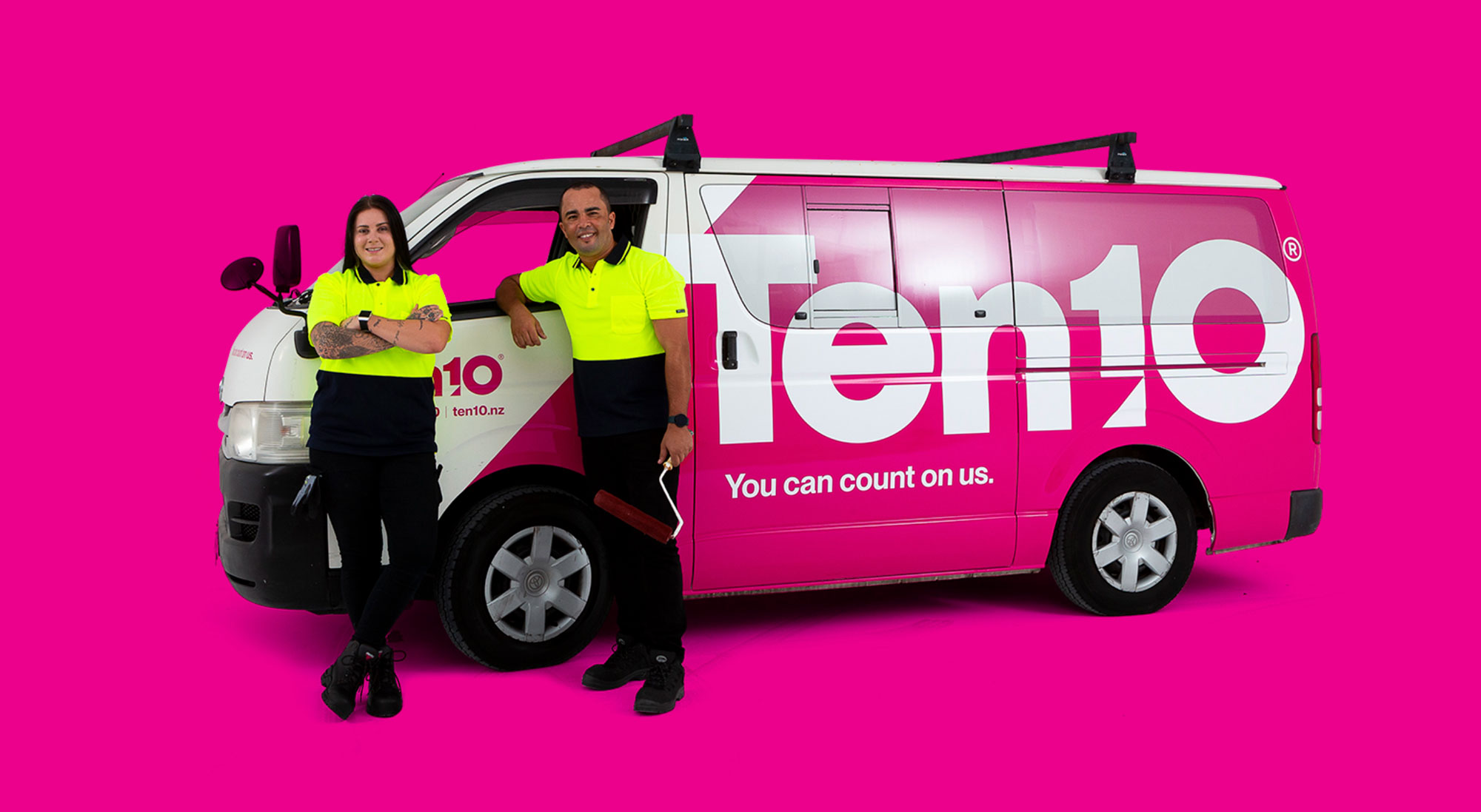
1:09
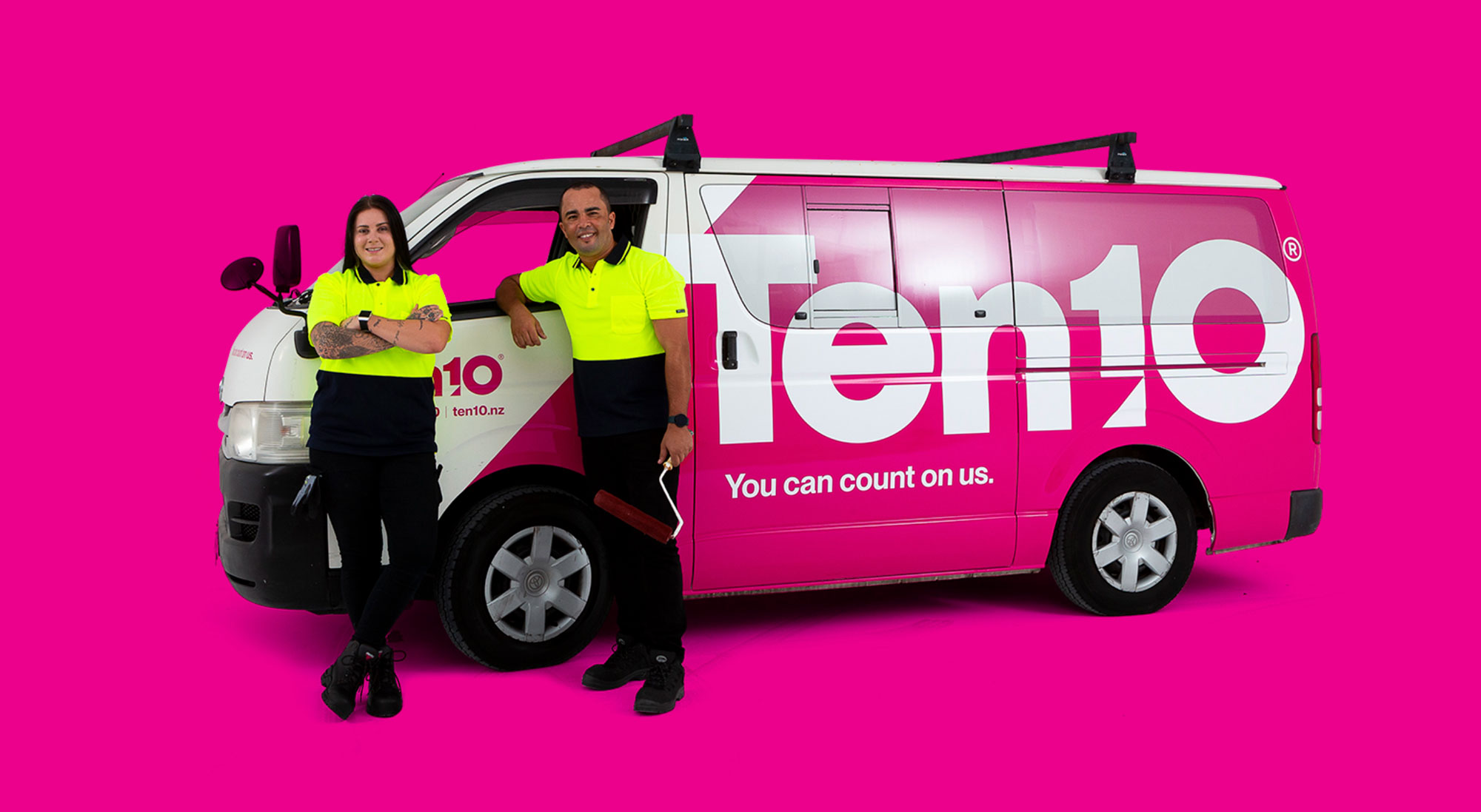
1:03
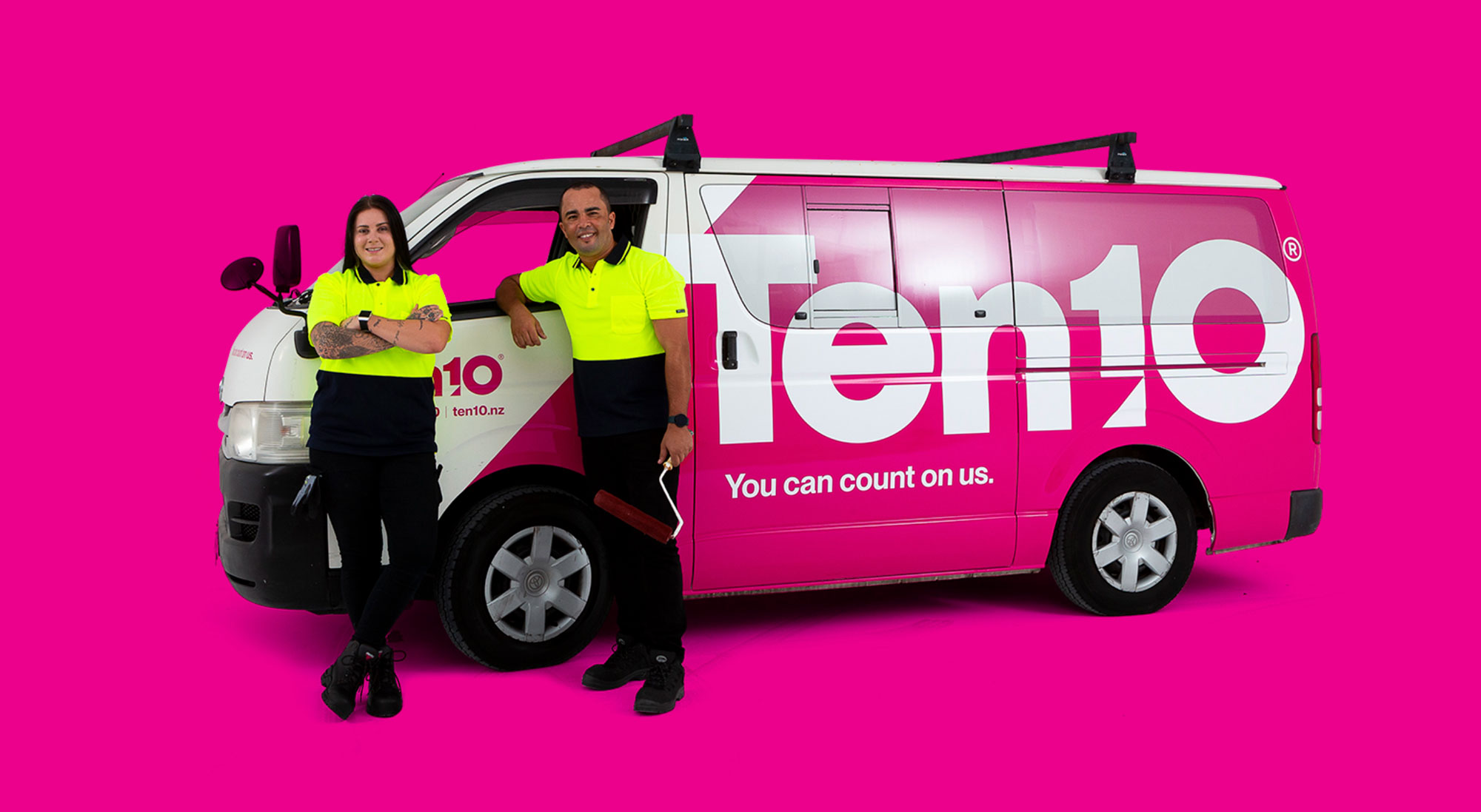
0:59
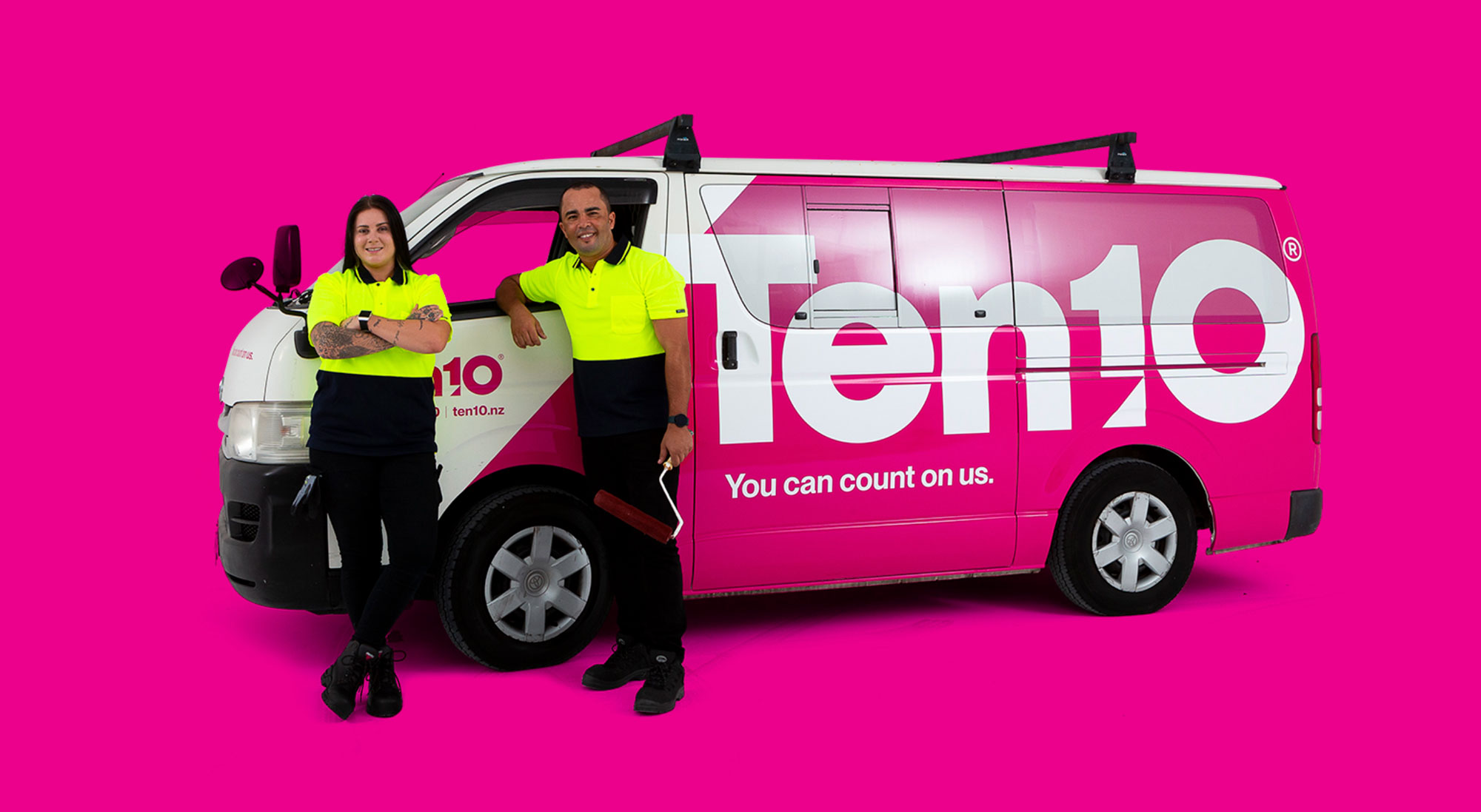
1:34
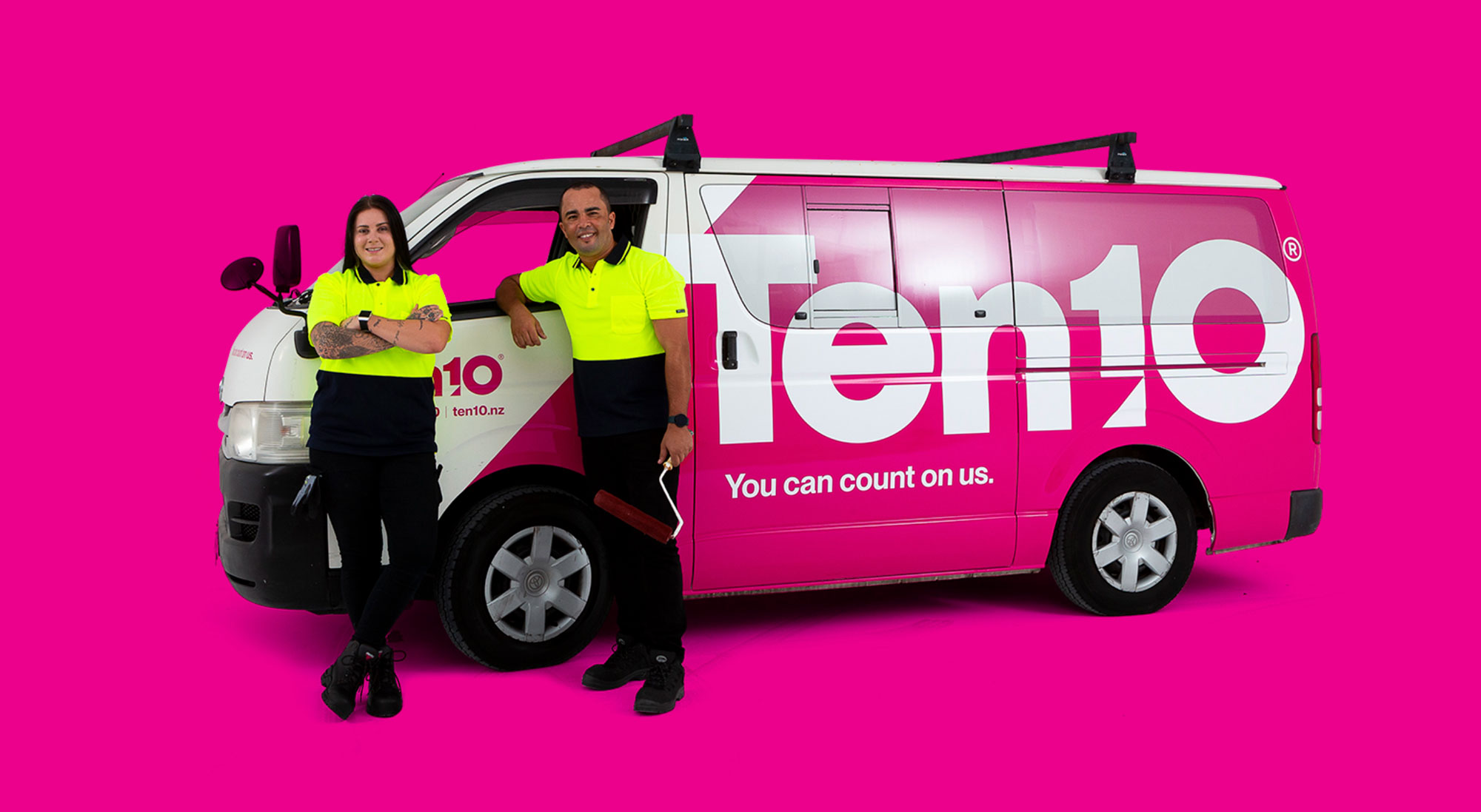
1:11
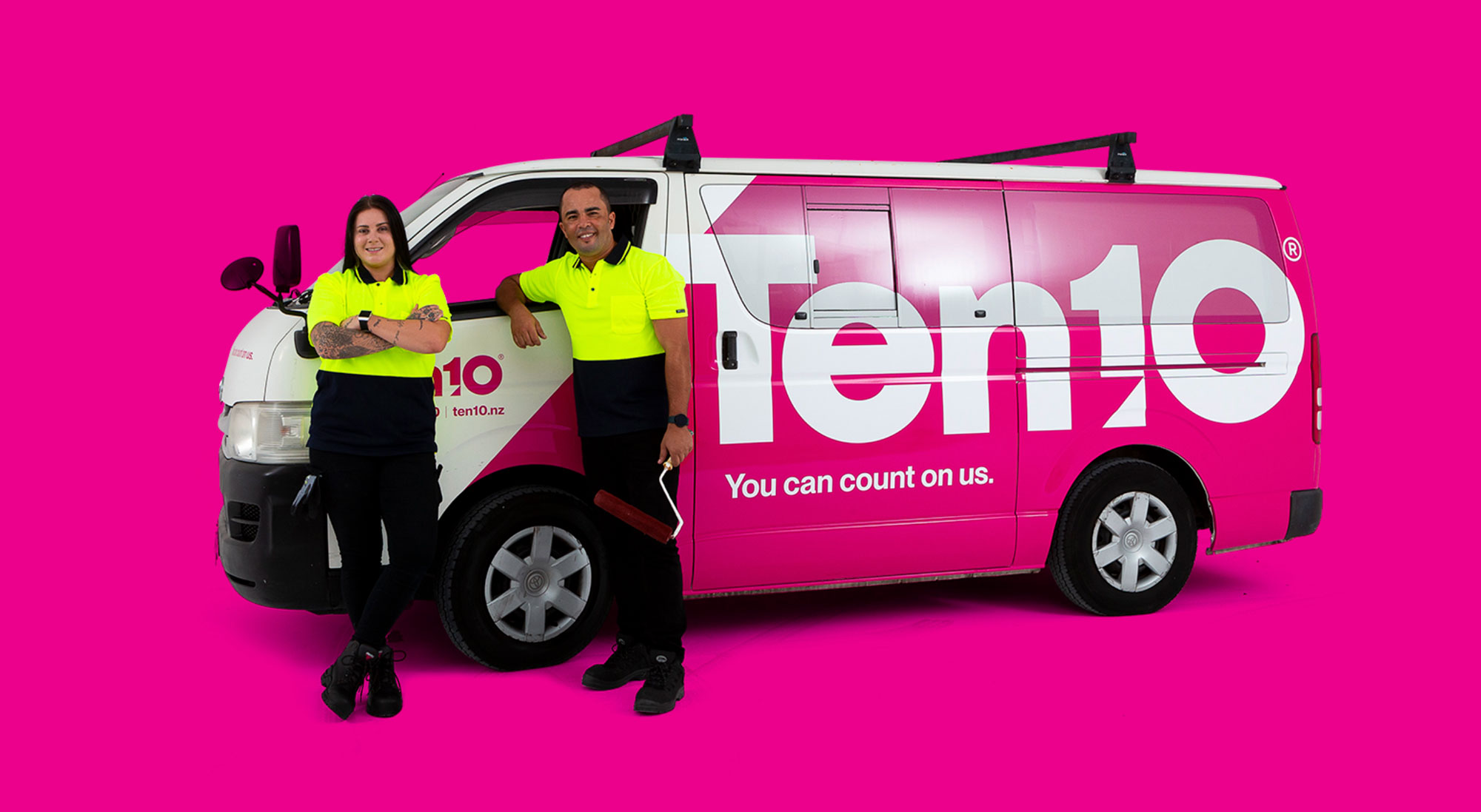
1:27
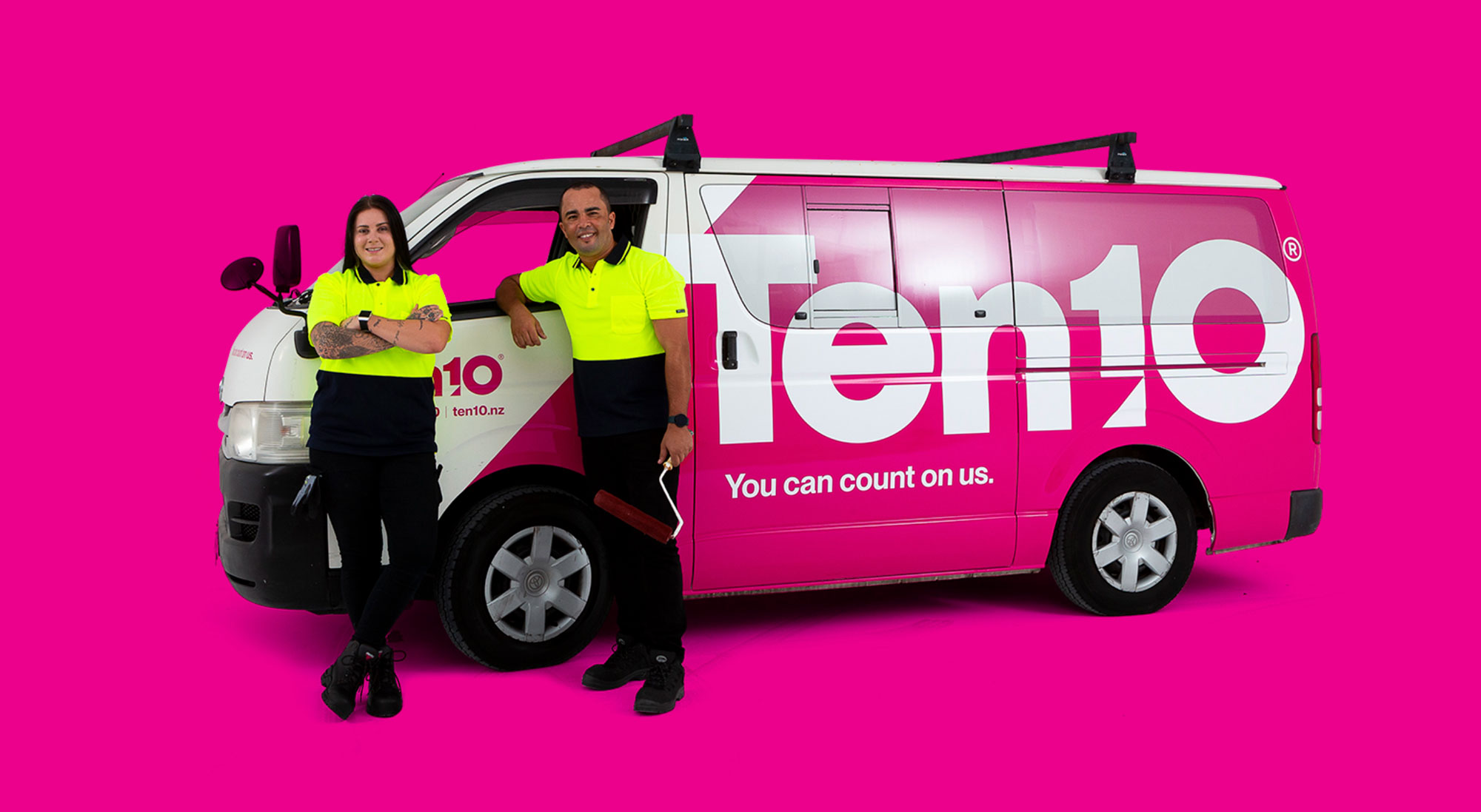
0:55
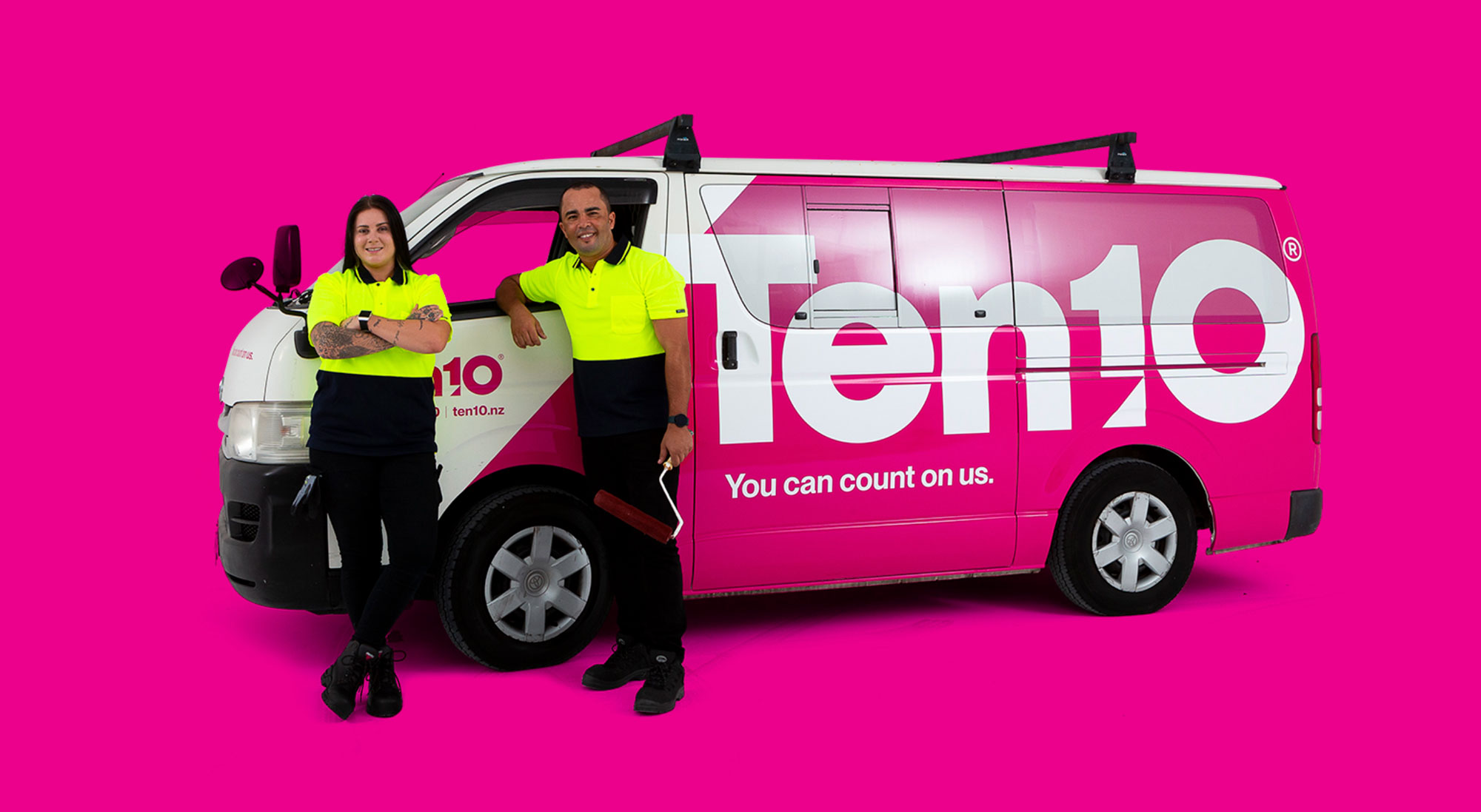
1:15
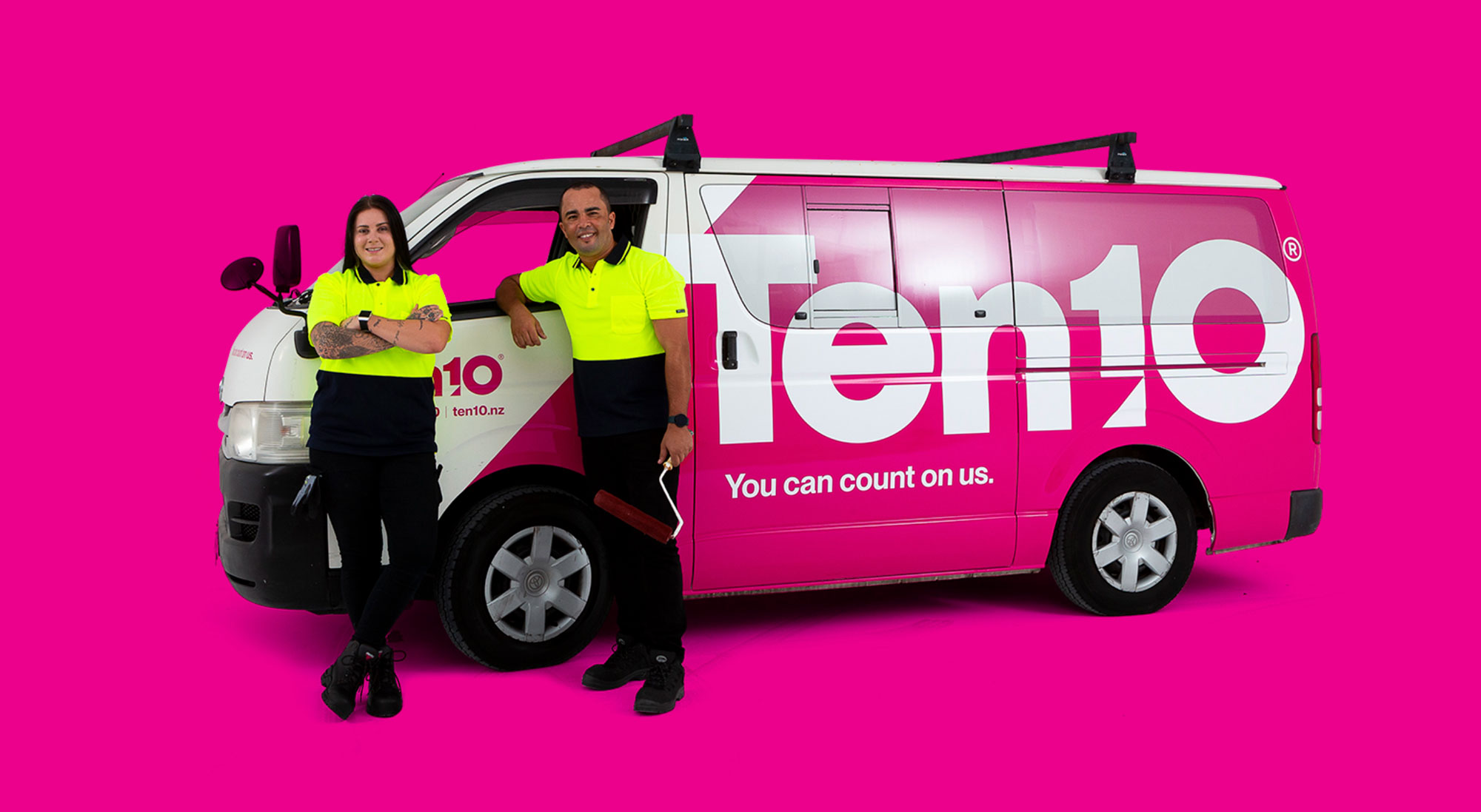
1:04
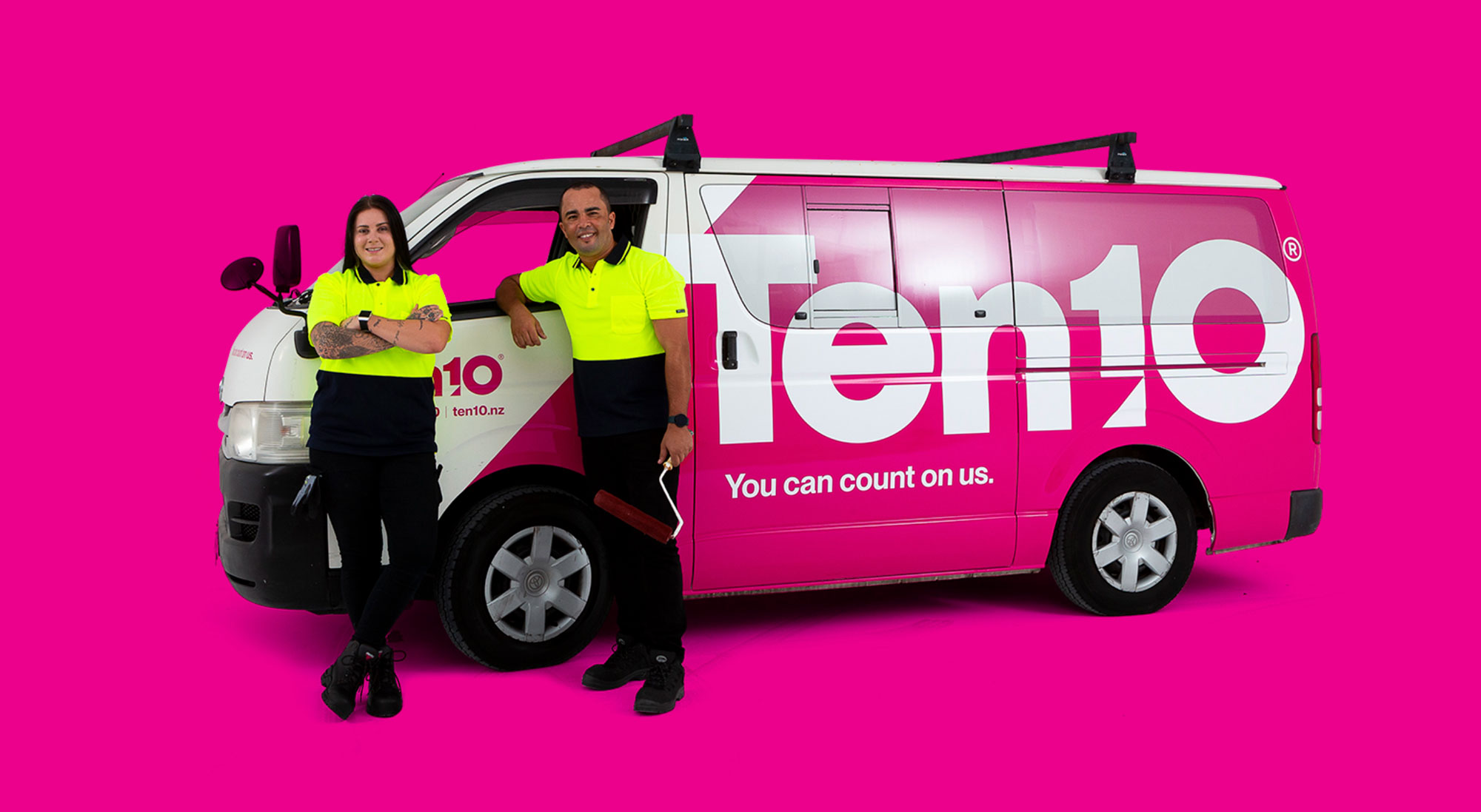
1:04
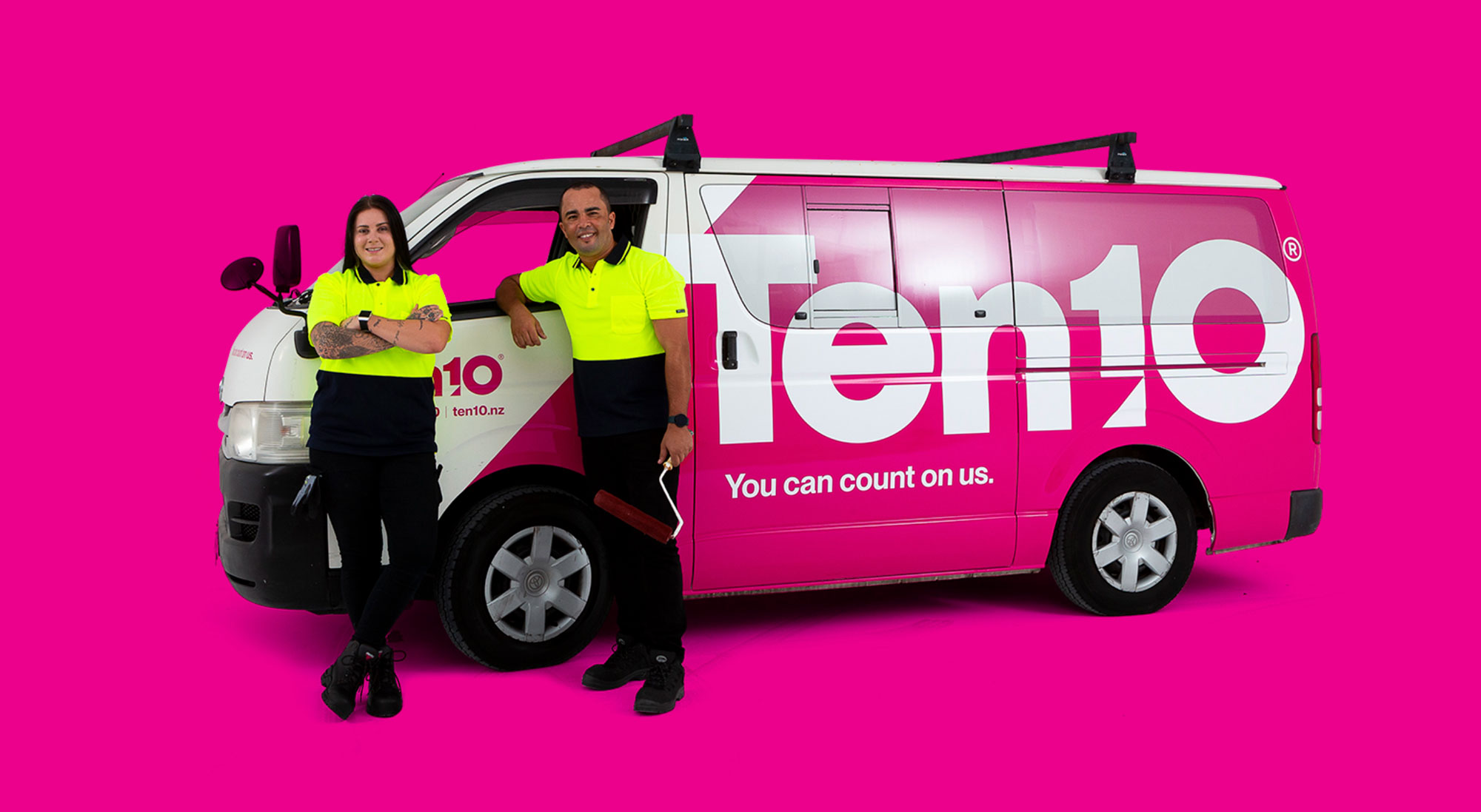
1:04
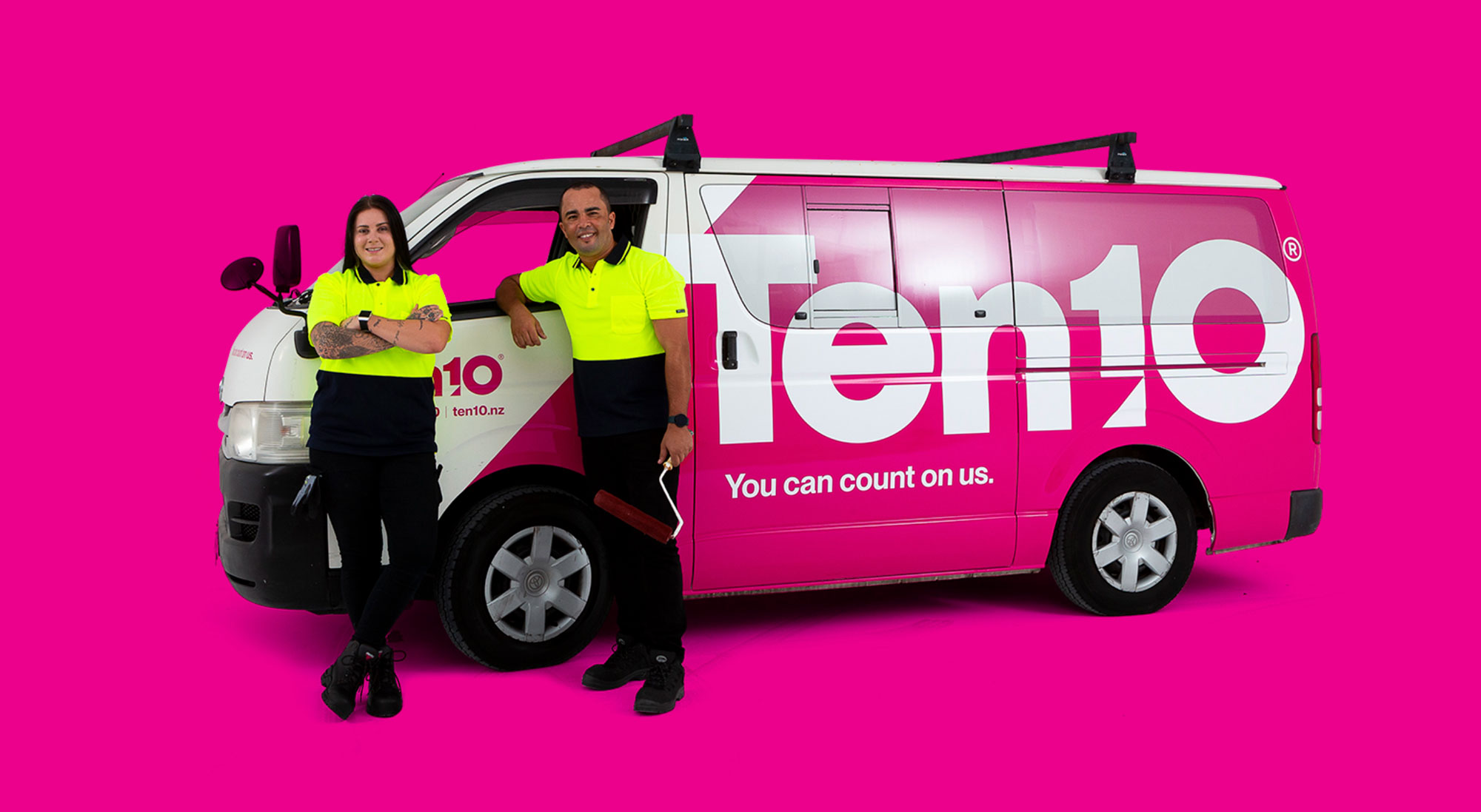
0:56
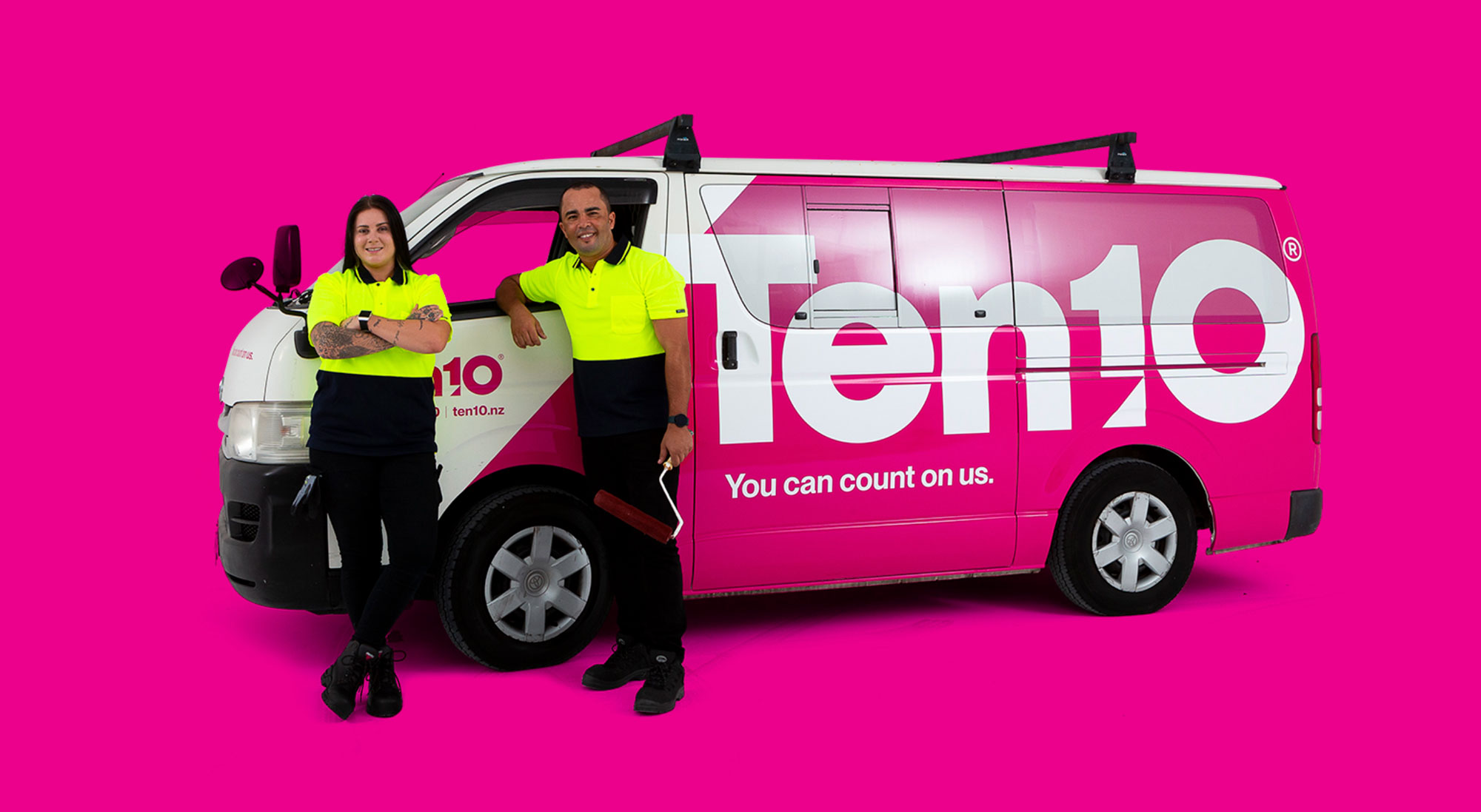
1:05
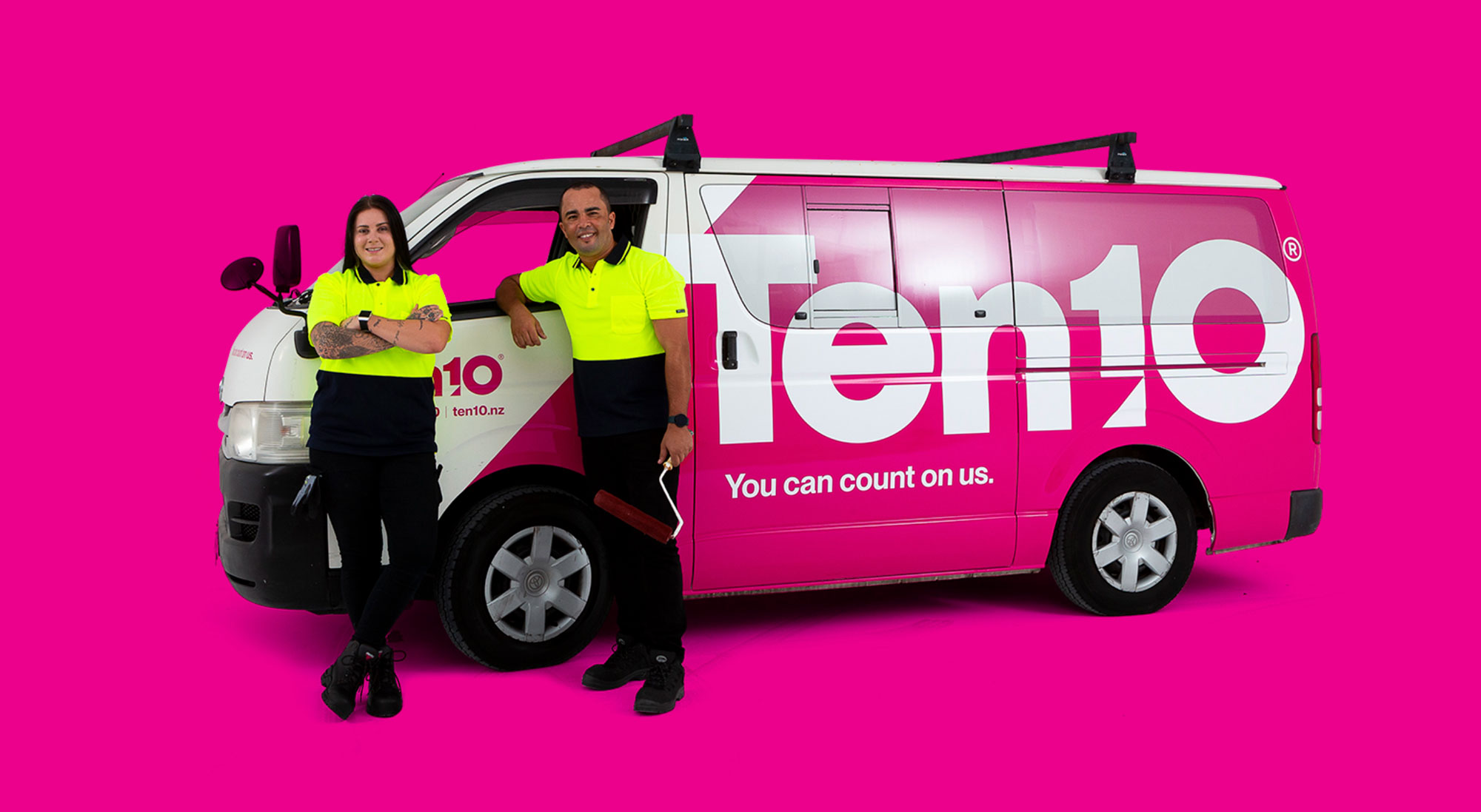
1:26
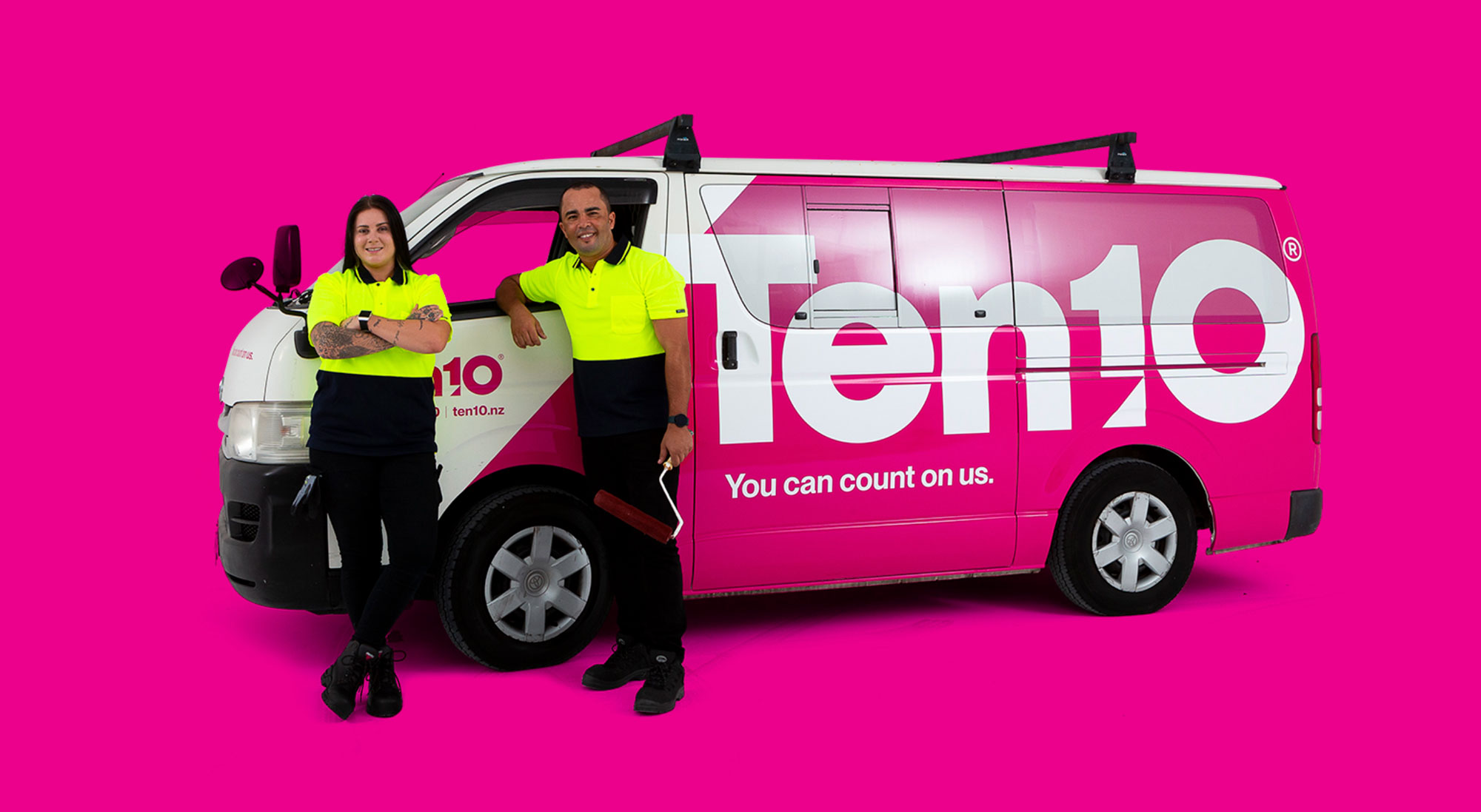
1:12
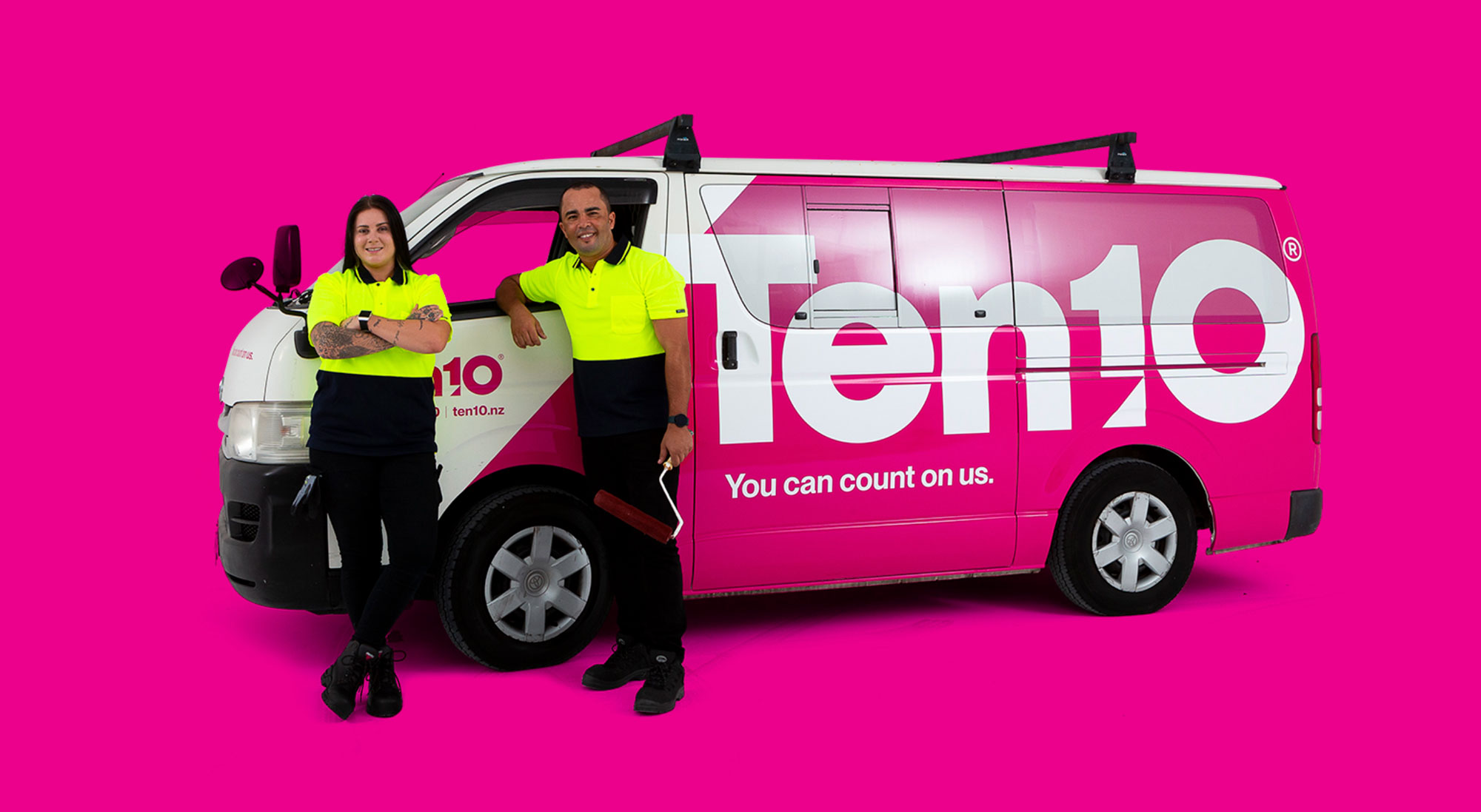
0:38
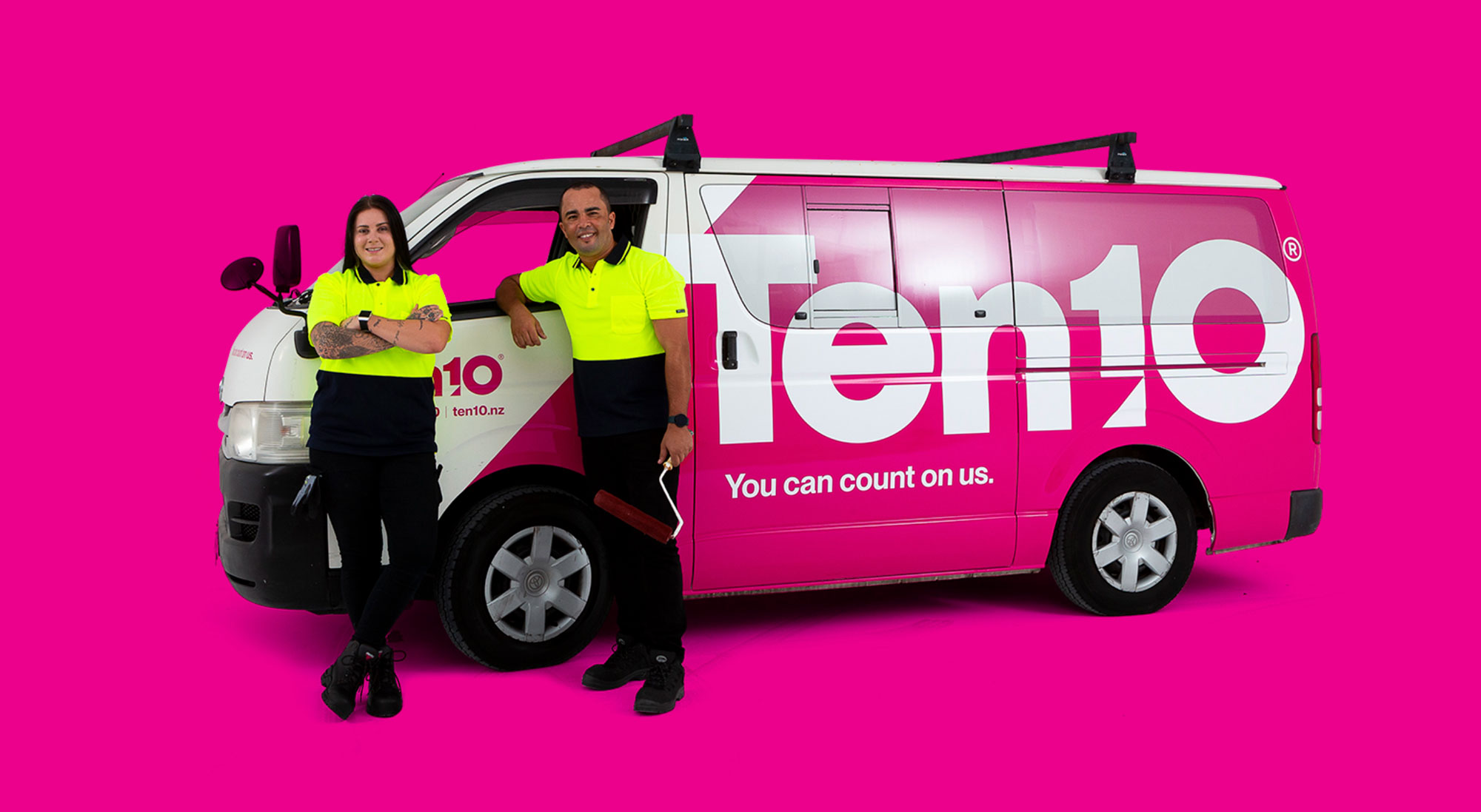
1:18
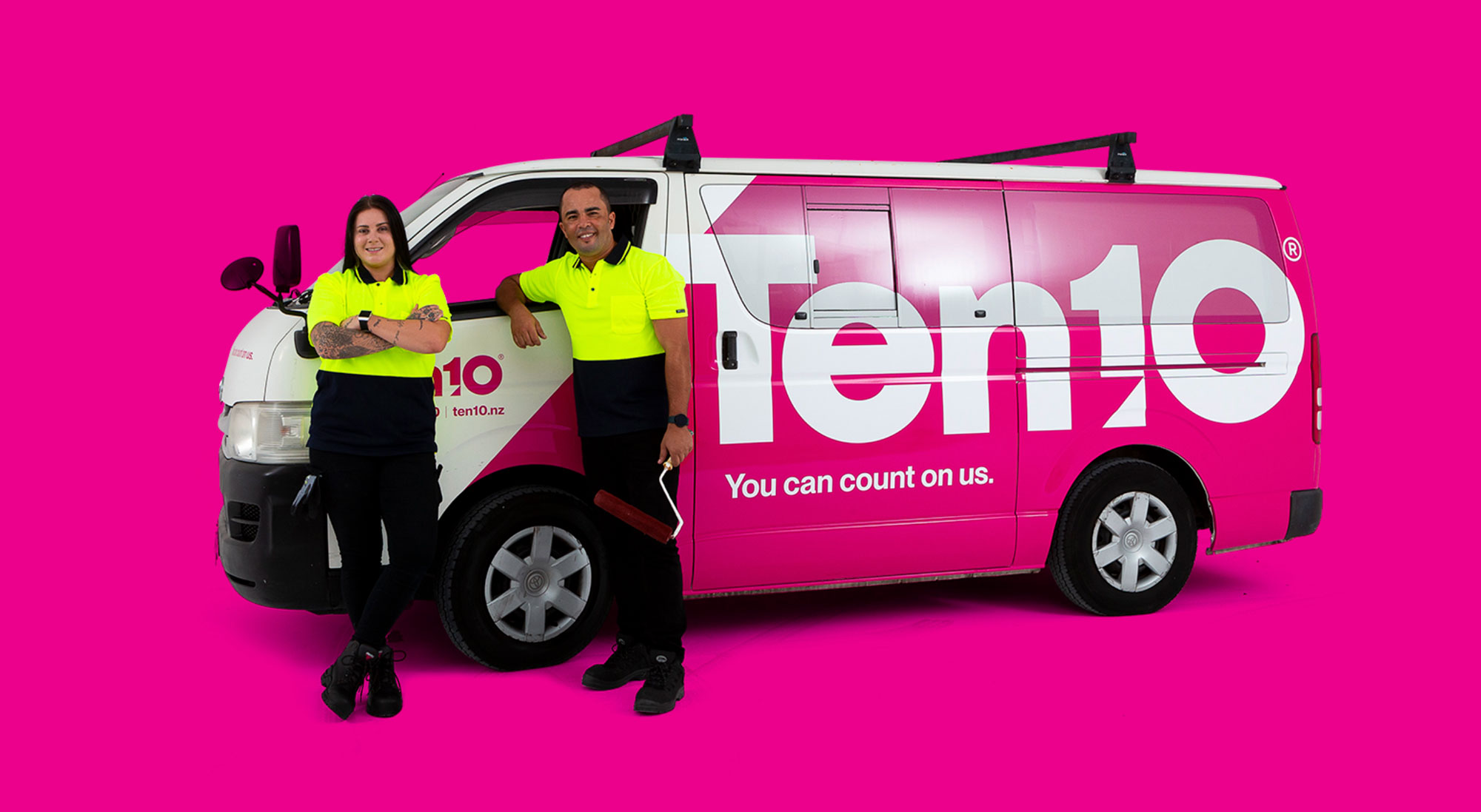
0:51
Add some content for each one of your videos, like a description, transcript or external links.To add, remove or edit tab names, go to Tabs.
The FAQs
Ten10 supplies Commercial and Industrial painting services to clients throughout the Auckland region. We specialise in large difficult access sites, such as ports, universities, and companies or clients with assets or properties spread over the region. An example could be FM companies, or councils.
Our point of difference is our people plus our processes which gives our customers operational excellence. We often get asked ‘what’s our favourite projects?’ We always say something large, high, and challenging.
Ten10 means many things. 10 out of 10. 100%. I had a saying for years – if you’re not a 10 don’t come to work. Get it right or don’t do it. Work hard play hard culture… you get it. It’s quite simple. Our fourth value is 10-10 all the time, work ethic, attitude and commitment. Let’s not forget as well it’s the police code they say over the radio for the most serious emergencies and somehow, Ben 10 the cartoon comes up a time or two – but let me promise you that’s not where it came from and I’m not a big fan of that.
Ten10 plans all projects out thoroughly, following checklists and processes to ensure the right outcomes are met.
We say great people plus great process gives us operational excellence. So for large, difficult sites seamless integration with Ten10 normally involves process mapping of the steps required. This process can start from daily signing, reporting procedures, site access methods and processes, through to understanding the key performance indicators of the client such as safety and job reporting. We then create a customised dashboard to display the site’s KPIs. There you have it, the Ten10 difference.
Quality Reporting is taking a snapshot in time of the stages of the project. I always say imagine no Quality Reporting. Typically cleaning, preparation, priming, and then top coating are stages of general repainting.
Now for Industrial Coatings it can include testing for salts, surface profile, coating thicknesses, adhesion testing. Along with that you have testing for dew point, surface temperature at the Industrial level – a good reason why house painters are not okay for steel works.
In short Quality Reporting gives client confidence and peace of mind.
I’m Ben Waite and I’ve been in the Painting and Industrial Coatings trade since I was 10 years old. Look I did go to school but I came out at 17 leading painting projects over the South Island. I love painting and talking coatings, always happy to meet and chat, and I have a real passion for solving coating problems.
I often decline the work if we’re not the best suited to make it good. I’m all about getting it right the first time.
The most challenging projects I’ve done are repainting cranes at ports, fuel tanks at tank farms, large bridges, and let’s not forget chairlift towers at ski fields – and what I say is after doing these everything else is easy.
My knowledge covers all aspects of painting from the industrial flooring market, waterproofing, sealants, industrial coatings, polyureas, polyaspartics including the lightweight plaster renders and I’ve even had time creating epoxy paints.
I’m going to share my biggest mistake in history – Pak and Save Rotorua. We must note that it’s still a client of ours, but one of our leaders in 2017 put two pack paint on without the hardener… the rest is history. Anyway we tried to remove it but a full re-clad of the front of the store was the only option to make it good.
I say follow the process you’ll get it right. If you stuff up, review your findings and learn. Thank you.
What annoys me, in fact it’s a pet peeve, tenants getting stung with penalties as they vacate their commercial property. These can be for unfinished repairs, make good not done correctly, perhaps some swollen cabinetry that they’ve missed. I created my three-point checklist on vacating your commercial property.
Step number one, check your contract. Review your contract and create a list of possible make good items then review this list with specialists from that trade. This could be construction people, HVAC specialists, corrosion consultants and so on.
Step two, ask who’s moving in and what they are likely to do. Finding out what the next tenant will do can allow for cash settlements for some areas. These areas often settle for a lot less than the complete make good costs.
Step three, invite the landlord for a walk around and agree on the make good list. We often consult clients on the fine print of these contracts it’s understanding the details accurately often means heaps less making good of the site and savings of thousands of dollars
Typically these are inspections by qualified coating inspectors. These inspections have two main reasons; to monitor the application and the prep process of a coating install, and to assess the coating condition and establish why failure has taken place.
Tests can include coating thickness, salts present on the surface, measuring the adhesion or the surface profile however the key is in establishing the reason behind the corrosion, and the ability to suggest a suitable specification.
We often consult on corrosion matters as it’s a passion of mine to investigate coating failures. We work closely with an adhesion scientist as well for complex remedial cases. Long-term best results come from knowing the correct coatings as well as how to apply them in a particular environment.
Typical buildings built from concrete, plaster, or iron can be easily recoated in the typical household brands. This includes the likes of Resene, Dulux and Wattyl – all have options of general house paint or elastomeric which is more suitable for fine surface cracks. However if your building has more extensive cracking we encourage more serious brands for these surfaces. An example could be like Equus or Sto where larger cracks can be bridged without the need for crack injection.
With any repaint the key is the chemical cleaning. If cleaned properly then the paint will stick very well to aged surfaces extending the repaint cycle by up to five years. We often help clients with these assessments and what systems and specifications are best suited depending on the surface condition.
Often companies will apply anti-graffiti paints to the lower three meters of buildings for an obvious reason, to allow the easy removal of graffiti. The main issue here is painters often overlook this product and paint over it with water-based paints. This results in coating failure. This is why it’s important to identify at specification time or before recoating, has anti-graffiti being used? If so, what base is it? And this will determine what primer will be required. Common primers include epoxies and etches.
We often review specifications for clients and suggests different primers and solutions to ensure that coating delamination is prevented.
Behind every flaking roof or surface is a reason. Failure to establish the reason means the flaking is sure to repeat itself. Here are some common reasons why roofs flake and delaminate:
- Poor preparation originally.
- Lack of cleaning.
- Lack of moss/lichen treatment.
- Lack of film build – perhaps they’ve done a one coat wonder.
- Could be a colorsteel breakdown, like a factory issue.
- And let’s not forget Calcium Plumbate Primers you can review in my video on this called ‘Old coated roofs – why are they failing?’
Poor prep on a roof repaint can massively increase the future costs through maintenance, let alone if corrosion gets away on the surface of the iron.
Coating failure can be a number of factors (watch my video on why is my roof flaking). However a common issue with older roofs is the old calcium plumbate primer that was used extensively in the 1970s to 1990s. This primer, which was very good for corrosion, after 30 plus years is breaking down under the surface of coatings causing paint failure and serious delamination.
Often overlooked and not known about by most paint reps this product is lead and under a microscope is dusty, so prep and priming must be different from typical flaking roofs. Cleaning and prep must include three thousand to five thousand PSI water blasts, plus brooming the surface to remove the dust particles – and the same day priming with etch primer. When we are doing inspections we often see this at power stations, universities, hospitals, schools, and even older dairy factories. Now remember this is a lead-based coating so containment is needed before high pressure cleaning gets underway.
Believe it or not you’re more likely to die walking down the street from something falling on you, then abseiling. Trained Abseilors have stringent checks and measures for health and safety hence safety is not the biggest risk. However from a quality point of view the saying stands true – what happens on ropes stays on ropes. Working on ropes is a challenging job. Nothing is steady, the wind is blowing and it’s not possible to do tasks as easy as if you’re standing on your own two feet.
We often give clients options so they can weigh up the risks of abseil versus other access methods, the likes of scaffold, and the cost versus quality benefits, including potential disruptions. To give you an idea a recent project was 30 percent more to scaff versus abseil.
A large concern for every hotel manager is how to repaint with minimal disruption to guests. Scaffold poles over windows, along with many other issues, do annoy guests and as a result bad reviews are uploaded far too often.
Some questions we consider with hotel repaints are;
- Can the site be accessed without the need for scaffold? If not can we get away without scaffold poles over the windows?
- Can we work section by section and close off those rooms whilst the works are underway?
- Can works be completed when the hotel is quiet with low occupancy?
- Can we add bold signage to the hotel outlining what’s underway? Communication always helps.
- Finally, can the project happen during work hours to minimise disruptions?
At Ten10 part of our service is making sure your hotel can still give the views to your customers that they paid for, minimising disruption to your guests.
Ten10 sets the benchmark for Industrial and Commercial painting performance in Auckland. We specialise in large difficult access sites like ports or universities and companies or clients with assets or properties spread over the region such as FM companies councils and large property owners.
Our point of difference is our people plus our processes, which give our customers operational excellence. With a non-negotiable commitment to the highest standards, we make sure Auckland looks its best. You can contact us via our website or on 0508 44 1010.
No, is the short answer here. In general repainting can be done in a selection of five ways. I have listed these in the order of what’s most cost effective.
- Mobile scaffold which can go up to two stories.
- Boom lifts or knuckles where it’s quick and easy for shorter heights up to 50 meters max.
- Swinging stages, where a stage is erected on the roof and lowered over the edge of the building.
- Abseiling, men on ropes – you can watch my video on the pitfalls of this method.
- And scaffolding as a last resort due to its cost.
We often give clients cost options. Let’s say they had building repairs to be done before painting – we would run the cost difference versus practical ability of doing the repairs, to help with the decision-making process. Another large consideration would be preparation, containment of flakes, and blast media.
Are you sick of hearing this? We’re talking about typical building repaint situations. A good option here is using two Dulux products. These products use concentrated levels of titanium pigment. For exteriors; Weathershield Super Hide, or interiors WashandWear Super Hide. These are interior and exterior options that will cover in two coats every time. If it doesn’t it’s an applicator fault. Of course they will never admit to that!
Limitations of these products: they’re slightly more expensive per litre, Dulux competitors will say it won’t last in the UV but I don’t go with that. Dulux tests everything very rigorously before putting it on the market. Try it today. Help your painter. Tell them how to do it!
Often seen is paint failure on weatherboards. The reasons for this include:
- Poor preparation (maybe even years ago),
- Dark colors used – where the expansion and contraction is massive,
- Poor quality boards splits etc, (filler won’t last in cracks on weatherboards),
- Too many coats of paint… Yeah seems funny but the more coats of paint they get the more chance they will flake right back to the substrate.
- Water-based coatings over the old oil-based system – they move at a different rate in the sun and just pop off.
- Water coming from above, perhaps a missing flashing somewhere, bubbling the paint off.
I often walk away from weatherboard projects if the client doesn’t want a long-term solution as I can’t handle seeing failed boards after two years.
Every company makes mistakes, let’s face it, but it’s what they do to make good. So I say start with a backwards plan. Ask for a project they stuffed up and find out what they did about it. Look at what sort of work they normally do like not much point using a house painter on a bridge. Go by your gut feeling what do they look and feel like? Any messy details around scope or inclusions are a real red flag for me. Consider, how long do you want it to last for? Is there a guarantee? And lastly focus on cost justification not the cheapest price.
There’s hundreds of paints on the market so what do I use? House paint belongs to Resene, Wattyl and Dulux. Specialist coatings for steel are the best from Altex-Carboline or Akzonobel and let’s not forget Wattyl’s industrial paint range.
However there are other factors you should consider before jumping right into painting… like how will the prep be achieved, lifetime value, proximity to the sea, or some other corrosive environment. A paint specification will generally cover the prep methods available, and from here the coating applicator can select what method he will use. We often consult with clients over the specification for the projects as this is critical for long-term success.
Let’s face it everyone knows what a water blaster is. However, water blasters have many variables including the PSI, or pressure, the water volume per minute, and the nozzle used. Three thousand PSI machines are used often in the painting space to clean down buildings. However roof cleaning before recoating or steel work needs a minimum of 5000 PSI at 23 liters a minute to give the best chance of success. After a thorough water blast of 5000 PSI what’s defective, or loose, is going to expose itself allowing proper preparation before recoating.
Water blaster nozzles include the straight jet and the turbo nozzles – the main difference is a turbo spins, creating a cutting force on the surface removing any loose material and creating the effect of another thousand PSI. To make sure you get a good job done ask your roof or steel painters what PSI machines they’re using.
Paint breaks down in the sun’s UV rays at so many microns per year. The darker the colour, or the brighter the colour, the worse the breakdown. Cleanliness of the surface also plays a part. High corrosive environments near the sea, or even in Rotorua from sulphur, six-monthly washdowns are key. Resene has always been a leader in the bright colours, however the last few years has seen Valspar or Wattyl with new technology called hydrochroma tinters, which not only covers better but lasts longer for brighter colours. Roof colours such as blues, greens, typically last longer if the correct film build is put on and the paint not thinned to excess during application.
To lower breakdown or fading I recommend the use of high quality exterior paints, close management of the application process, and regular building washing.
My personal preference is either using Dulux, Resene or Wattyl for walls and roofs, but for steel work Altex/Carboline would be my favourite. Altex specialist steel coatings are far superior to the mainstream systems.
Why Altex? Well I personally prefer that because I used to use these products from a young age and you know how they apply best and what you can and can’t do.
Prep to weatherboards is done in a variety of ways, often with a tungsten scraper on the defective areas. Here are some steps to prep weatherboards properly for painting.
- Chemical clean surfaces using sodium hypochlorite.
- Remove all defective paint a tungsten is okay paint stripper is better.
- Take the paint back to a hard solid edge.
- Apply Resene Timberlock
- Leave to dry for 24 hours.
- Prime the boards with an oil-based wood primer.
- Leave to dry for 24 hours and then fill the hollow areas or the low areas with contract filler.
- After this the top coats can go on.
If using a high gloss top coat prime the filler before recoating it. This way the lifespan of your coating will be hugely increased. We often review with clients the options of re-clading versus poor condition weatherboards as splits in boards will not last the test of time.
What a question and so often asked. In general the lighter the colours the better, so a white or a cream has the same lifetime value as such, but a dark grey or a forest green – the breakdown is a lot faster. Bright colours are the worst for breakdowns this is due to the tints used in them. An example would be like The Warehouse – the red sheds, Beaurepaires sites, Pak and Save yellow. To sum up, light colours is best, followed by dark colours, as in forest greens, denim blues, and lastly bright shades.